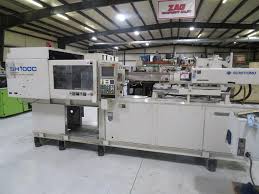
Understanding Molding Machines: Types, Functions, and Applications
Molding machines are essential in various manufacturing automatic injection molding machine industries for producing parts and products from materials like plastic, metal, rubber, and ceramics. These machines shape materials into desired forms by using molds. This article delves into the types, functions, and applications of molding machines, providing a comprehensive understanding of their importance in modern manufacturing.
Types of Molding Machines
There are several types of molding machines, each designed for specific materials and applications. The most common types include:
- Injection Molding Machines
- Blow Molding Machines
- Compression Molding Machines
- Rotational Molding Machines
- Transfer Molding Machines
Injection Molding Machines
Injection molding is one of the most widely used processes for manufacturing plastic products. The machine heats plastic pellets until they melt, then injects the molten plastic into a mold under high pressure. Once the plastic cools and solidifies, the mold opens to release the finished part. This method is ideal for producing large volumes of parts with intricate shapes and fine details.
Key Applications: Automotive parts, consumer electronics, medical devices, and household goods.
Blow Molding Machines
Blow molding is a process used to create hollow plastic parts, such as bottles and containers. There are three main types of blow molding: extrusion blow molding, injection blow molding, and stretch blow molding. In each method, plastic is heated and formed into a parison (a preform), which is then inflated within a mold to take the desired shape.
Key Applications: Beverage bottles, containers, and plastic drums.
Compression Molding Machines
Compression molding is used to create large, flat, or moderately curved parts. The process involves placing a pre-measured amount of material into a heated mold cavity, then closing the mold to compress the material into shape. This method is commonly used with thermosetting plastics and composites.
Key Applications: Automotive parts, aerospace components, and electrical insulators.
Rotational Molding Machines
Rotational molding, or rotomolding, is a process used to produce large, hollow plastic products. The machine rotates a mold around two perpendicular axes while heating it. The centrifugal force ensures even distribution of the plastic within the mold, creating a uniform wall thickness.
Key Applications: Storage tanks, playground equipment, and kayaks.
Transfer Molding Machines
Transfer molding is similar to compression molding but involves an additional step. The material is first placed in a chamber, heated, and then transferred into the mold cavity using a plunger. This process is often used for encapsulating electronic components.
Key Applications: Electrical components, seals, and gaskets.
Functions of Molding Machines
Molding machines are designed to perform several key functions to ensure the efficient production of high-quality parts:
- Heating: The machine must evenly heat the material to a precise temperature suitable for molding.
- Molding: The material is injected, blown, compressed, or rotated into the mold to form the desired shape.
- Cooling: The molded part must be cooled to solidify and retain its shape.
- Ejection: The finished part is ejected from the mold, ready for any post-processing steps.
Applications of Molding Machines
Molding machines are crucial in various industries due to their ability to produce complex and precise parts efficiently. Some primary applications include:
- Automotive Industry: Production of bumpers, dashboards, and various engine components.
- Consumer Goods: Manufacturing of toys, household appliances, and packaging materials.
- Medical Devices: Creation of syringes, surgical instruments, and diagnostic equipment.
- Aerospace: Production of lightweight yet durable components for aircraft.
- Electronics: Manufacturing of casings, connectors, and insulating components.
Conclusion
Molding machines play a vital role in modern manufacturing, enabling the production of a wide range of products with varying complexity and precision. Understanding the types, functions, and applications of these machines helps appreciate their importance in different industries. As technology advances, molding machines continue to evolve, offering even more efficient and versatile manufacturing solutions.
By comprehending the capabilities and applications of molding machines, manufacturers can make informed decisions to optimize their production processes and meet the demands of their respective markets.